TOTO小倉第一工場、小倉第二工場見学
TOTOさんのご協力のもと、福岡県北九州市のTOTO小倉第一工場、小倉第二工場を訪れました。当社のお客様もTOTOブランドに対する信頼は厚く、その要因となっている「高品質な製品」がいかにして作られているのか、工場見学のレポートを通しご紹介いたします。
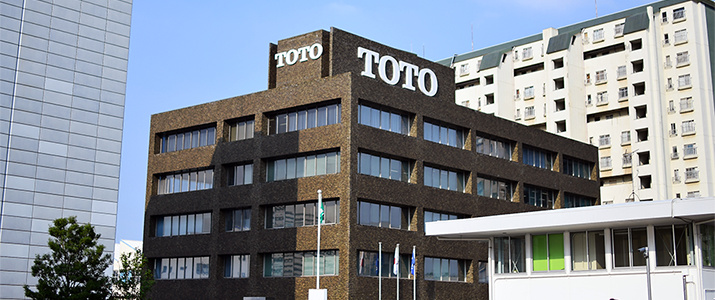
衛生陶器開発のパイオニアとして、業界のトップを走り続けるTOTOは、1914年に国産初の陶製腰掛水洗便器の開発に始まり、今日に至るまで、セフィオンテクト、トルネード洗浄、きれい除菌水、エアインシャワー、エコシングル水栓など、多くの特許技術を開発しています。
住宅設備専門店の当社としても、機能性・品質・デザイン性に優れたTOTO製品は、"長く使える良いもの"をご希望されるお客様に対しても自信を持ってご提案することができ、実際に、当社で施工・購入されたお客様からの満足度も高くなっています。
TOTO社是に掲げられている「良品の供給」と「お客様の満足」。
創業以来100年の歴史を支える、高い品質の製品を生み出す製造現場・製造工程を通して感じたこと、TOTOアクアテクノ・TOTOサニテクノの方々から伺ったお話をレポートいたします。
TOTO 小倉第二工場
まずは小倉第二工場を訪問いたしました。
小倉第二工場は1967年に設立され、主に、水栓金具・電気温水器・手すりなどの開発、製造が行われています。ウォシュレットや浴槽など、小倉第二工場から生産が始まった製品も多いそうです。
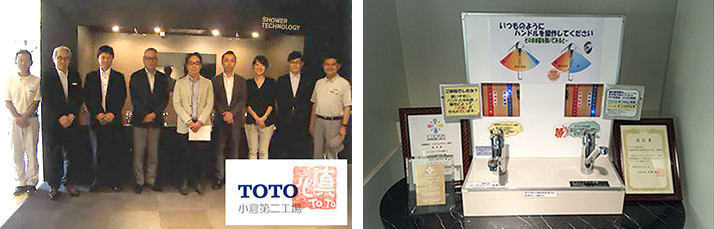
小倉第二工場の一角には、水栓の展示室があり、当社でも人気のエコシングル水栓の仕組み、エアインシャワーの使用水量を目で見て違いを確認できる装置や、海外市場に供給されている水栓なども見ることができました。
いよいよ工場内の見学です!
今回は水栓金具(蛇口)の製造過程を見学させていただきました。
(工場内は撮影禁止のため、ここから文章のみでお伝えいたします。)
水栓金具ができるまでの工程
これまで見学させていただいた住宅設備関連の工場は、ベルトコンベアーで流れてきた部品を組み立てるライン生産方式でしたが、TOTO工場では、部品をピッキングして組み立てる生産方式で、他工場との違いを感じました。
生産は以下の順に行われておりました。
- ①鋳造:砂を固めた型に溶かした金属を流し込み、蛇口の原形を作る
- ②機械:加工機械で、原形の蛇口のバリを削ったり、ネジ穴を開ける
- ③研磨:研磨用ベルトで表面を削り、外観形状の仕上げを行う
- ④めっき:サビ防止と、傷防止のために、金属メッキを施す
- ⑤組立:給水、排水用の管などの部品を取付け、製品として完成させ、検品する
それぞれの工程で感じた、ものづくりの”こだわり”をご紹介します。
匠の技術の継承(鋳造・機械・研磨)
工場内は多くの工程が機械化されており、蛇口の原形を造る鋳造工程では銅合金を溶解炉に入れる作業・溶かした合金を型に流し込む作業、蛇口の外観形状の仕上げを行う研磨工程ではロボットアームがスピーディーかつ細やかな動きで研磨作業をこなしておりました。
現在では、大量に生産される製品は、一連の研磨作業を機械によって行っていました。以前は手作業で1個1個研磨しており、当時は1日140個の研磨作業が限界だったところ、複雑で緻密な研磨の動きをロボットにプログラミングし機械化したことによって、今では1日400個の研磨が可能となっているそうです。
現在でも、高級価格帯の製品など、機械での研磨が難しい製品は、手作業で研磨が行われているそうです。研磨は水栓の形状と外観の品位が決まる重要な作業工程のため、高度な技能をもつ技能士・特級技能士が担っています。そういった技能の向上や、技術の伝承を図るため、スペシャル制度を設け、匠の技術を次の世代に継承する仕組みづくりがなされていました。
見えないところにも高品質(めっき)
研磨された状態の、めっき加工前の蛇口は五円玉のような色をしています。その状態の製品に、サビ止めのニッケルめっき、その後にキズ防止のクロムめっきをすることによって、シルバーのピカピカの状態となります。
TOTO水栓は、JIS規格で定められているめっき加工の厚みより、さらに厚く加工が施されているそうです。これによって、メッキがはげにくくなり、より長く使用できるようになっています。
また、設置した状態では見えない部分にも、サビ・キズ防止の加工が施されていました。こちらは小便器用の洗浄水栓を半分に割ったもので、外側だけでなく、水が通る内側にも錆が出ないようにコーティングが施されています。このコーティングも、お客様に良いものを、安心して、より長く使ってもらいたいという思いが込められています。
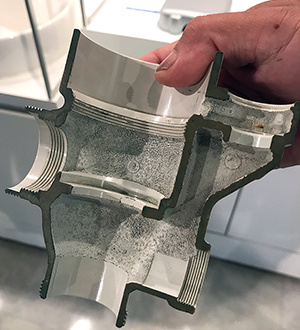
生産ラインの中で無駄を省く工夫(組立)
組立の作業は、コンベアーでの流れ作業ではなく、必要な部品をピッキングして組立てる方法で行われていました。流れ作業よりも品質が保てるとの理由で、ピッキング方式で組立が行われているそうです。
初めて作業する方でも間違わずに部材等のピッキングができるように、部材の保管位置が決まっている「定位置管理」や、すぐに完成品の抜き取り検査ができるように、組立作業のすぐ近くに検査・検品するスペースがあったりと、無駄を省く工夫、品質を維持・向上させる工夫を随所に感じました。
TOTO 小倉第一工場
次に、TOTO本社の隣にある、小倉第一工場を見学いたしました。
1917年に設立された小倉第一工場は、小便器や大便器などの衛生陶器の製造、また、工場の隣ではウォシュレット等の開発が行われています。
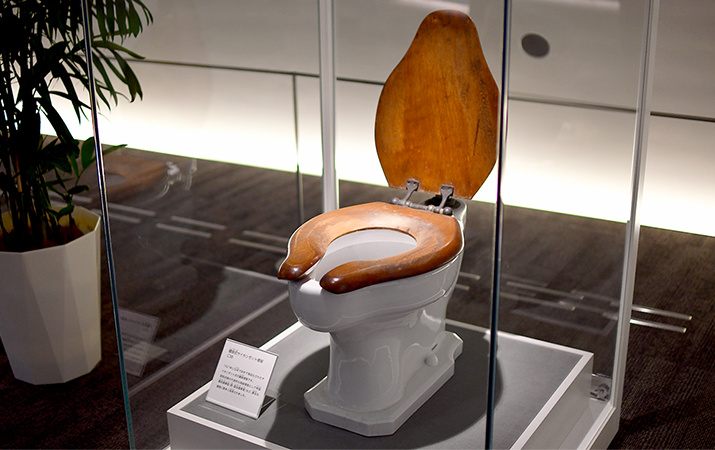
1927年に日本で初めて商品化された腰掛便器(TOTOミュージアムで撮影)もこの小倉第一工場で製造されました。
いよいよ工場内の見学です!
今回は衛生陶器の製造過程の7工程あるうちの5工程を見学させていただきました。
(工場内は撮影禁止のため、ここから文章のみでお伝えいたします。)
衛生陶器ができるまでの工程
これまで見学させていただいた住宅設備関連の工場は、ベルトコンベアーで流れてきた部品を組み立てるライン生産方式でしたが、TOTO工場では、部品をピッキングして組み立てる生産方式で、他工場との違いを感じました。
生産は以下の順に行われておりました。
- ①調整:原料と水を混ぜ合わせて陶器の材料となる泥漿(でいしょう)を作る工程
- ②成形:泥漿を型に流し込み、形を作る工程
- ③乾燥・生素地点検:成形した陶器の原形を乾燥させる工程
- ④施釉:陶器に色や艶が出るよう、釉薬を全体に吹き付ける工程
- ⑤焼成:施釉した製品を焼き上げる工程
- ⑥検査:焼き上げた製品に欠陥がないか検査する工程
- ⑦組立・梱包:付属品等をセットし、梱包する工程
今回は②~⑥までの工程を見学いたしました。
衛生陶器製造の原点、小倉
衛生陶器は、原料である陶石・長石・粘土など20種類以上もの天然素材と水を混ぜ合わせ機械で粉砕し、泥状の泥漿(でいしょう)という液体で作られています。原料となる陶石や長石など一部の素材が展示してあり実際に触ることができましたが、大きさや質感がそれぞれ全く違うものでした。
それらの原料は6割が国内、4割がイギリス・中国・韓国などの海外から入手されているそうです。創業当時から陶石(とうせき)などの原料は海外より輸入しており、小倉は原材料の輸入の便が良かったことに加え、『燃料の石炭が採れる筑豊炭田に近い』『完成した商品を輸送するための拠点となる門司港に近い』という点で、事業に最適の地だったようです。
創業より100年、変わらず小倉の地で衛生陶器が作られており、創業時から受け継がれる「ものづくりの心」を感じました。
陶器は製造過程で大きく縮む
工場入口に、大きさの異なる大・中・小の3台の男性用小便器が並べられていました。ほぼ同じ見た目ですが、本来水平であるはずの部分が上に膨らんでいたり、色が違うそれらは、成形工程後の小便器(大)、乾燥工程後の小便器(中)、焼成工程後の小便器(小)を比較した展示でした。
衛生陶器は、“どろ(泥漿)”を製品の型に成形した状態から、乾燥で3%、焼成で10%、合計で13%の縮みが発生するそうです。本体が大きい衛生陶器は、重力の影響を受けやすく、部分によっても収縮率が異なるため、あらかじめ変形を加味して成形され、焼き上がった際にきれいな形になるよう計算し製造されているそうです。色も乾燥と共に変化をしていました。
陶器のため、焼く前と焼いた後で大きさが変わることは想像していましたが、想像以上に大きな縮みが発生することに驚きました。
高価格帯の衛生陶器は1台1台手作業で作られている(成形)
衛生陶器の形が作られる成形の工程では、陶器の材料となる泥漿を型に流し込んで成形を行います。流し込む型は、「石膏(せっこう)型」と「樹脂型」の2つがあり、それぞれの特徴を生かし、生産する商品によって使い分けられていました。
成形した製品を型から外した後は、1台ずつ手作業で形が整えられていました。高価格帯の便器は、最適な水流を生み出したり、洗浄性能を高めるために、内部が複雑な形しているそうです。ネオレストの成形では5つほどのパーツを、泥漿を接着剤代わりにしてパーツ同士を繋いだり、水をつけたスポンジで繋ぎ目を滑らかにしたりと、複数のパーツを人の手で組み合せることによって形が作られていました。機械化が進んだ中でも複雑な部分や肝心な部分は人の手で造られていて、陶芸で作品を作っているような作業に、思わず見入ってしまいました。
繊細で細やかな感覚と受け継がれる技術(乾燥・生素地点検・施釉)
成形された製品は、均等に乾くよう、乾燥室でゆっくりと時間をかけて乾燥されます。乾燥後の段階で、型から外した大きさよりも3%縮んでいます。この段階で、かすかな傷があっただけでも製品としての耐久性に影響するため、細かなひび割れやキズ、凸凹がないか、肉眼による厳しい検査をする「生素地点検」が、一つ一つの製品に行わていました。
生素地点検に合格した製品は、陶器に色付けと艶を出す釉薬(ゆうやく)を吹きつける施釉の工程に移ります。施釉工程では、熟練の職人さんの手の動きをプログラミングしたロボットアームによる「ロボット施釉」と、人がろくろで製品を回転させながら釉薬を吹き付ける「手がけ施釉」を見学しました。
ロボット施釉は、1台にかかる施釉スピードが早く、量産生産に適しており、熟練技術者の方の動きがインプットされているだけあって、その"腕裁き"は滑らかでした。
手がけ施釉は、形状が複雑な製品や、小ロット製品でおこなわれており、作業者の方はいとも簡単に均等に釉薬を吹き付けているように見えましたが、熟練の繊細な技が必要とされているそうです。展示されてた、施釉に使用するスプレーガンを操作してみたところ、指の力加減が難しく、細やかな感覚で均等に吹き付ける技がいかに高度かわかりました。
衛生陶器の外観の美しさは、この釉薬をいかに均一に吹き付けるかという技術にかかっているそうです。ムラなく釉薬を吹き付ける技術は、長年に渡り受け継がれてきた熟練の技であり、TOTO独自開発の釉薬で陶器表面をツルツルに仕上げる汚れの付きにくいセフィオンテクトも、こういった工程で、人の手で作り上げられていることが分かりました。
また、目に見える部分だけでなく、製品内部の排水の通り道にも釉薬が吹き付けられていました。これは、内部にも汚れを付けず、少ない水でもしっかりと汚物をスムーズに流せるためのもので、手間をかけても質の高い製品を作る、ものづくりの魂を感じました。
施釉工程の最後にTOTOのロゴマークを手作業で付けていきます。便器に向かって左下奥の側面にあるロゴマークは、釉薬が乾いた後に一つ一つ手作業で、シルクスクリーンを使用し、染料を擦り付けられており、曲がって付けてしまうと、これまでの作業が台無しとなってしまう、とても緊張感のある工程でした。
信頼の高品質は人の手による全数検査(焼成・検査)
施釉後、TOTOロゴマークがつけられた製品は、全長115メートルのトンネル窯の中を24時間かけて焼き上げられています。この工程で、焼き上げ前の乾燥した状態から、さらに10%の縮みが発生します。
窯の中は一定の温度を保っているわけではなく、中心は1150℃以上にも達っする一方で、急速に温度を下げる場所があったりと、焼く工程にも様々な工夫がされていました。
焼き上げられた衛生陶器は、成形の状態から合計13%の縮みが発生します。金属やプラスチックなどとは異なり、品質のコントロールが難しいとされる陶器。そのため、焼き上げられた衛生陶器は全ての製品を対象に、全数検査を行っていました。寸法が定められた大きさになっているか、ひびや割れがないかの検査が、人の手によって行われていました。
検査項目は、外観検査、寸法検査、打音検査、から洗浄試験や排水試験などの性能チェックまで数多くの厳しい検査が行われています。見学中に聞こえた、コンコン、カンカン、陶器を木づちで叩く「打音検査」が印象的でした。これは陶器内部にひびや割れがないかを音で聞き分ける検査工程で、外観には問題がなくても、内部でひび割れがあると音が鈍く聞こえるそうです。
打音検査の体験コーナーで実際に音の聞き分けを体験しましたが、音は本当にかすかな違いで、叩く部位がずれていれば正常な音がすることもあるそうで、割れを見逃さずに検査するにも技術が必要だと感じました。
成形から完成までに、度重なる検査を全てクリアしたものだけが製品として出荷できるということからも、高い品質を保つ"ものづくりの心"を感じました。
TOTOミュージアム
最後に、2015年8月に開設されたTOTOミュージアムを見学しました。創業100年の歴史や、歴代の水まわり商品を実際に見ることができます。
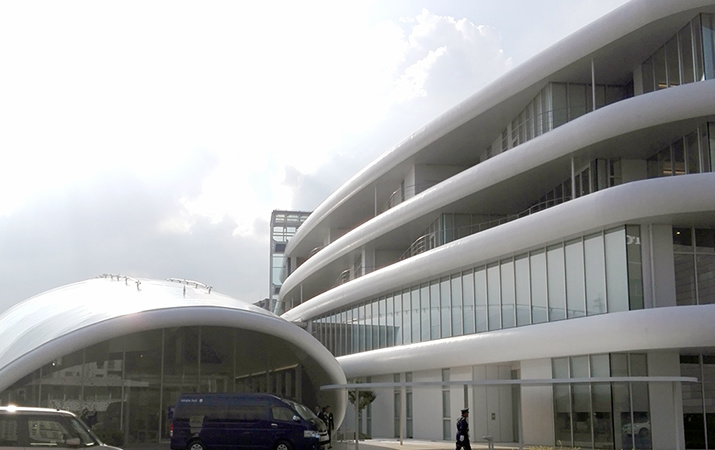
TOTOは、欧米の進んだ生活文化に触れた創立者の大倉和親氏が、日本にも「快適で清潔な生活空間の提供したい」との思いから、衛生的な水洗便器の製造・普及を目指し、東洋陶器株式会社として設立されました。設立後40年間は事業を支えるため食器の製造も行っていたそうで、現在のTOTOロゴの色は、得意としていた食器の瑠璃色が使われているそうです。
TOTOミュージアムには、2万回以上の試行錯誤を繰り返して開発された国産初の「陶製腰掛水洗便器」や、1980年にトイレ設備の環境を一遍させた「ウォシュレットG」など歴史的価値を認定された商品が展示されています。
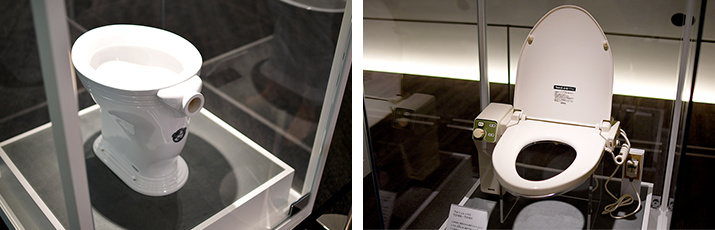
今では当たり前の水栓トイレですが、TOTO設立の1917年当時は共同の汲み取り式トイレを複数の家庭で共用し、下水道さえ整っていなかったそうです。衛生的な水栓トイレを各家庭に広めたいという想いは、当時は革新的すぎて実現には大変な苦労があったのだろうと想像します。
おわりに
今回の見学にあたり、TOTO様・関係会社様など、多くの方々にご協力いただき、また、こちらからの多岐に渡る質問にもひとつひとつご対応いただき、誠にありがとうございました。
工場で働く方々、製造工程を通し、TOTOさんの高品質へのこだわり、そして常にお客様を第一に考えるものづくりの姿勢を、とても印象的に感じました。
また、トイレを製造している小倉第一工場では、製造過程で不良になってしまった製品を陶器屑として再利用した路面材の製造を行うなど、製品を造るだけではなく、限りある資源を大切にする取り組みが行われ、「ものづくりの心」が長年にわたり受け継がれていることを身をもって感じました。
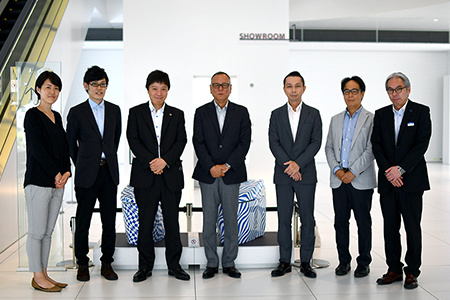
住宅設備工事販売専門店として、自信を持ってお客様にTOTOブランドの製品をご提案できるとともに、より良い製品の開発に寄与できるよう、サービスの向上に邁進してまいります。