ノーリツ・ハーマン工場
ノーリツコンタクトセンター見学
ノーリツさん、ハーマンさんのご協力のもと、主にガスコンロを開発・生産しているハーマン工場(大阪府大阪市)、主に給湯器を開発・生産しているノーリツ 明石工場(兵庫県明石市)、お客様からのお問い合わせを受け付けるノーリツ コンタクトセンター(兵庫県明石市)の3施設を見学して参りました。
■ハーマン生産工場の見学
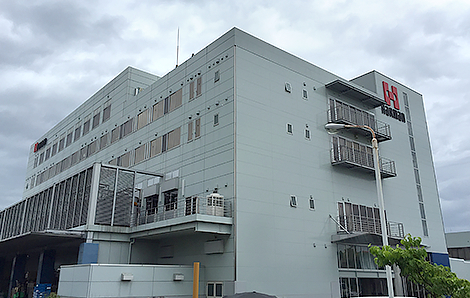
ハーマンは、ガスコンロや小型給湯器、浴室暖房乾燥機の企画・開発・生産・販売を行っている企業です。2001年にノーリツと業務提携をしてから、ノーリツグループの中核企業として主にビルトインガスコンロ等の厨房分野機器の開発・生産をしています。
ビルトインガスコンロなどの買い替え用の厨房機器は、2014年にノーリツブランドに統一されましたが、開発・生産は今でも、全てハーマンが担っています。

ハーマンは、創業当初から、業界初の技術・製品を数多く世の中に送り出してきた先進的な企業で知られています。最近でも、天板上にあるスイッチで指先ひとつで操作を行う「スマートコンロ」や、焼き網を使わずに多彩な料理を楽しめる「マルチグリル」など、既存の枠組みにとらわれない発想で製品を開発されています。
同時に、幅広い多くのお客様にハーマンの商品を手に取ってもらえるように、「安くていいものを」をモットーに、日々研究開発を重ねられているそうです。
工場見学用の帽子をかぶって、皆で記念写真を撮影したら、いよいよハーマン工場の見学です。
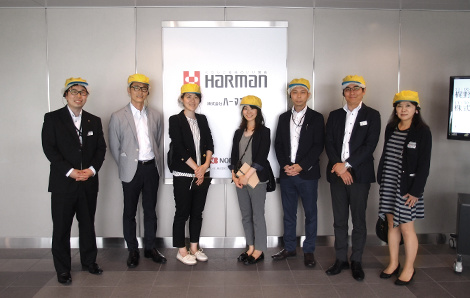
ハーマン独自の生産システム「HPS」
ハーマンの工場では、ビルトインガスコンロ・テーブルコンロ・浴室暖房乾燥機・小型湯沸かし器の4商材、全1200種類を生産しています。開発から設計、部品組み立て、出荷まで全てこの工場で行います。
東京ドーム1個分ほどの敷地で、住宅設備機器の工場としては、それほど大きな規模ではないとのことでした。「狭い敷地の中でいかに効率よく生産するか、常に考えています」とのことで、効率的に生産するためにHPS(Harman Production System)という、受注した商品を、受注した順に生産するシステムを導入している、との説明がありました。このHPSは、「必要なときに、必要な商品を、必要なだけ生産する」という考え方に基づいた生産システムなのだそうです。
住宅設備は、壊れてしまってから交換を依頼するお客様が多く、「新しい機器に交換するまでの期間に、不便な思いをなるべくさせたくない」、「いち早く商品をお届けしたい」との思いから、必要な商品をはやく納品できる仕組みを作るため、このHPS方式を生み出したとのご説明がありました。
工場内で見た生産ラインの様子
工場の中に入り、生産ラインを見学しました。高級価格帯の製品を製造するライン、普及価格帯の製品を製造するラインと、大まかに分かれているものの、受注した順番に生産していくため、ラインに流れてくる商品はバラバラで、全く同じ品番の商品が続けて流れてくることは、ほとんどありません。
実際に普及価格帯のガスコンロを生産しているラインを見せていただきましたが、「ファミ」の次に「右高火力のメタルトップ」、次に「温度調節機能ありのメタルトップ」、続いて「左高火力のメタルトップ」・・・と、次々と異なるコンロが組み立てられていました。
次々に異なる品番のガスコンロがラインに流れてきますが、取り付ける部品と、取付け位置が異なるため、間違いのないようコンロに貼ってある指示書を元に素早く組み立てていきます。
各組み立て担当者の後ろに、1~10番まで番号のついた棚が並べられており、その棚にラインから流れてくる10品番分の部品が、取付ける順番通りにセットされていました。
担当者は、セットされた部品を順番に取付けることで、製品を正しく組み立てていくことができるようになっています。
事前に使用部品がセットされていますが、担当者ごとに、その部品が本当に合っているのか、指示書通り組み立てられているのか都度確認しながら、スピードをもって確実な作業をされているのが印象的でした。
さらに、工程ごとにも、それぞれのコンロに貼られた指示書通りに部品が組み立てられているかのチェックが必ず行われており、1台のガスコンロが生産されるまでにたくさんのチェックを重ねていることがわかりました。
高い品質を目指して
ハーマン工場のスローガンとして、「業界No.1の品質を目指す~未来に残そう 品質と信頼~」という言葉が掲げられていました。
1台1台生産している商品が異なるため、各部品がそれぞれ正しい位置に正しく組み立てられているか、正常に点火するかを、機械による検査を行ったあと、最終チェックとして、人による目視での検査が行われており、Wチェックが徹底されています。
人による最終検査では、炎の色がしっかり分かるように、少し暗い部屋で入念に行われます。この最終チェックは、高い技術を持った方しか行えないそうです。
ラインでも、品質管理のための工夫がされていました。従業員一人一人の頭上に黄色いランプがあり、流れてきた製品に少しでも問題があると感じた場合、ランプを点灯させれば、ライン長がやってきて、一緒に製品の不具合を確認してくれます。
さらに、月に1度、従業員の方々が、「どうすれば、自分の仕事を更に効率化できるのか?」「どうすれば、作業ミスをさらに減らせるのか?」などの業務改善提案を行ったり、工場内の美化を保つために、別のラインの作業場をチェックして、整理・整頓されていない場合は報告したりと、品質向上や業務効率化のために、従業員一丸となって日々取り組んでいるとのことでした。
工場見学のあと、ハーマンの商品開発部、生産部、ノーリツの営業部、マーケティング部の方々と意見を交換する場を設けていただきました。
上位機種に搭載されたマルチグリルを中心にお話を伺いました。
料理もお手入れも手軽になり、さらに「焼く」以外の用途でもグリルを使用できる「毎日使えるグリル」をコンセプトに、マルチグリルは開発されました。
マルチグリル搭載のコンロ(プログレ、スマートコンロ)を購入されたお客様からは、グリルの焼き網を掃除する必要がないことが便利で、お手入れ性が高く評価されているとのことでした。この話に、自宅でプログレを使用している当社のスタッフが食いついてきました。
当社のスタッフは、キャセロール(マルチグリル専用の蓋付き鍋)に煮汁を入れ過ぎて、吹きこぼしてしまったとのことで、「グリルの下火バーナーに滴下して、汚れてしまったのではないか?」「お手入れはどうしたらよいのか?」と質問をしていました。
担当の方によると、「キャセロールの底面にある凹凸が、キャセロールをつたって煮汁を下バーナーに滴下することを防ぐので、下火バーナーに直接煮汁は掛からない。 そのため、下火バーナー自体のお手入れは不要で、バーナー周りのグリル底面のみ拭くだけで大丈夫。」とのことでした。グリル庫内も手前に向かって傾斜するように設計しているため、煮汁が吹きこぼれた場合も、グリル手前側に流れやすく、掃除もしやすいそうです。
キャセロールでそうめんを茹でて、煮こぼれた時に下火バーナーに茹で汁がこぼれるのか、という実験をしたこともあるそうです。通常使用では、キャセロールで麺を茹でるのはNGなのですが、汁が最も吹きこぼれる調理方法が麺ゆでだったため、このような実験を行ったとのことでした。
実験の結果、キャセロールから吹きこぼれた茹で汁は、グリル底面に溜まり、下火バーナーにこぼれることはなかったそうです。
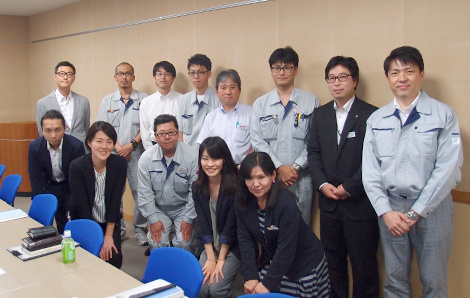
■ノーリツ 明石本社工場(NAM事業所)見学
続いて、ガス給湯器を生産しているノーリツのNAM(NORITZ AKASHI MESSE)事業所を見学しました。
追い焚き機能付きのガス給湯器・床暖房熱源機は、すべてこの工場で生産されています。
ノーリツの歴史
工場見学に入る前に、ノーリツの歴史と、これまで開発されてきた製品の展示を見ることができました。
終戦復興期の、いわゆるゴエモン風呂を使っていた頃に、「さめないタイル風呂」として、写真左のような「能率風呂」を発売したのが、ノーリツのはじまりです。
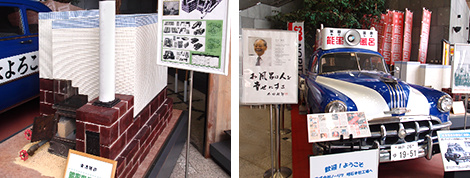
当時、この能率風呂を、写真右の車とノボリを使って、軍艦マーチを流しながら宣伝したそうです。
実際に車の上に能率風呂を乗せて走らせ、街頭の人が実際にお風呂を体験できるようにしたとのことで、その斬新な宣伝方法にとても驚きました。
これが、今では当たり前にみられる「街頭宣伝カー」の始まりだそうです。
ノーリツの創業者の太田会長は元海軍兵で、兵学校での辛い訓練の中、唯一の楽しみはわずかな入浴時間で、この時間にだけ生きていることを実感できたそうです。
そうした経験をもとに生まれた「お風呂は人を幸せにする」という太田会長のメッセージを原点に、能率風呂の開発から始まり、ガス風呂釜、湯沸かし器、給湯器の開発と販売をしてきたノーリツの長い歴史を知ることができました。
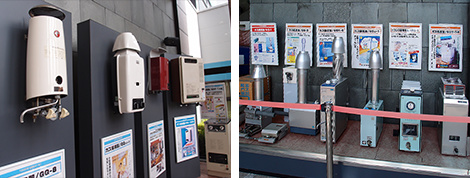
中国や台湾・アメリカで販売されている給湯器やガスコンロも展示されていました。デザインの好みや用途などが各国で異なるようで、様々なデザインの機器がありました。
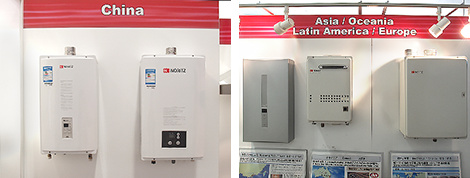
ノーリツは、生産拠点を中国にもっていて、給湯器の一部の部品は中国でも生産しています。これは、部品の生産を一極集中させるよりも、分散させて生産した方が、災害などがあった際も迅速に対応できるからとのことでした。
いよいよ、給湯器の工場見学です。
(工場内は撮影禁止のため、ここから文章のみでお伝えいたします。)
開発・生産にかかわる
全ての施設がそろった工場拠点
ノーリツの給湯器工場でも、ハーマンの工場と同様に、「必要な商品を、必要な分だけ、必要な時に生産する」NRPSという生産システムを導入しています。
給湯器は約1万種類もあり、この内の560機種は、工場に在庫としてストックし、いつでも受注できるような体制を整えているとのことです。
(※1日の出荷分の約7割は、この在庫から出荷するそうです)
また、明石工場(NAM事業所)には、給湯器の生産工場の他に、部品を製造するグループ会社、機器開発センター、実験棟、生産設備の技術開発センター、研修施設など、生産と開発にかかわる全ての施設がそろっているのも、他社にはない特徴です。
そのため、製品企画から開発・生産まで、スピードをもって対応できることも強みとのことでした。
工場内で見た生産ラインの様子
実際に、床暖房対応熱源機(GTH)の生産ラインを見学させていただきました。
床暖房対応熱源機は1ラインで作られていますが、この1ラインだけで4000種類もの機種を作ることができるそうです。
1機種完成までは、約75分で、1日約50台ほど生産しているとのことでした。
ハーマンの工場同様、ラインに流れてくるのは全て異なる品番の製品でした。この工場でも、部品を正しい製品に取り付けられるように、製品それぞれに貼られている指示書をもとに組み立てていました。
給湯器の部品は、グループ会社から仕入れているものもあるそうですが、その企業にも、給湯器の生産順に部品を並べて、40分に1回納品してもらっているとのことでした。NRPS方式は、グループ会社との綿密な協力の上で成り立っていることがわかります。
給湯器組み立てラインの細かい部品を組み込む工程や、リモコンの組み立てなど、細かい作業が多い工程では、作業者のほとんどが女性でした。
細かい作業を行なったり、細かな部分に気づくことができるのは女性の方が向いているとのことで、機器を組み立てた後の最終チェックも、ほとんど女性が行っていました。
精密な機械だからこそ、入念なチェック
給湯器本体も、リモコンも、たくさんの部品から成っていて、さらに部品一つひとつが細かい、精密な機械です。
この工場にも、ハーマンの工場と同じように、従業員一人ひとりの頭上にランプがついていて、なにか問題があると感じた時には、すぐにライン長を呼ぶことができる仕組みが導入されていました。多い時には1ラインで1日100回以上、ランプが点灯することもあるそうです。
給湯器本体もリモコンも、組み立て以上に入念に行われていたのが、製品組立中・組立後のチェックでした。
給湯器本体のチェックは、実際にガスを通して着火するかのチェック、給湯器内部の部品がすべて組み立てられた段階での機械によるチェック、それが終わると、人による目視での最終チェックが行われていました。
目視での検査ができるのは試験に合格した一部の人のみで、資格証が作業服にもつけられていました。
目視による最終チェックは最も入念に行われていて、部品が正しく組み立てられているか、ガス漏れは発生していないかのチェック項目を確認をしたあと、同じチェック項目をもう一度見直してから、ようやく合格となります。
リモコンの場合、回路の組み立ての途中までは機械が行い、細かい部品の取り付けは全て女性の手によって行われていました。その後、回路の防水・防汚のためのコーティングを施して、回路の最終チェックに回されるのですが、ここでは、機械と目視による検査が行われていました。
慣れによるミスを防止する
「いじわるチェック」
繰り返し作業の多い工場での「慣れ」によるミスを防ぐために、年に9回ほど「いじわるチェック」というのを実施しているそうです。
これは、従業員からの提案から始まったもので、わざと部品を外して、そのミスにしっかりと気づけるかどうかの確認を行っています。
いつ、いじわるチェックの対象となった製品が回ってくるかわからないので、そうした危機感から、どの製品もしっかりとチェックする意識が強くなったそうです。
いじわるチェックの他にも、類似部品を取り間違えないようにチェックする仕組みなど、従業員からの発案で導入された、ミスを防ぐための取り組みを紹介していただきました。
スピーディーな生産のために作業の効率化を進めると同時に、ミスなく的確に仕事をこなすための様々な業務改善のアイディアを、従業員の方がそれぞれ自発的に考え、実施されていました。
■ノーリツ コンタクトセンター見学
ノーリツのコンタクトセンターは、全国からのお客様のお問い合わせを受け付けているコールセンターです。
今回見学させていただいた兵庫県明石市だけでなく、東京都杉並区にもあるそうで、これも災害などのリスクに対応するため、2つの拠点に設けているとのことでした。
女性が多い職場とのことで、女性の意見を取り入れて施設づくりをされていて、とてもきれいでおしゃれな環境でした。コールセンターという職場柄、スタッフのケアやフォロー、働きやすい環境づくりに力を入れられているようでした。
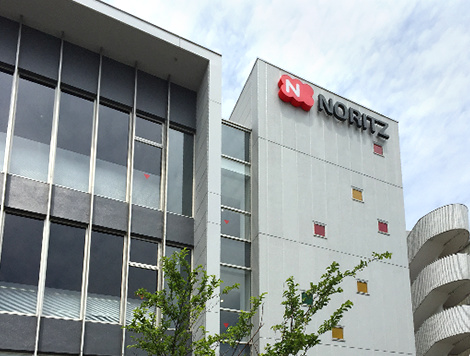
迅速・丁寧、ミスのない応対のために
お客様からの電話を受けるのは、主に女性のスタッフの方々です。始めに応対したスタッフが質問に答えられなかった場合、各商品に関する専門知識をもった技術スタッフが代わりに答えます。
各フロアの正面には、大きなモニターがあり、誰が、どのくらいの時間、電話応対をしているのか、また、電話を受けられるスタッフがどのくらいいるのか、コールセンターの状況が表示されていました。
上長がモニターを見て、電話が長引いているスタッフがいれば、応対に困っていると判断し、電話の内容を一緒に聞いてスタッフに指示を出したり、電話を代わるなど、状況を見ながら、各スタッフをサポートします。
また、各スタッフは、応対した電話内容の概要を文字に起こし、記録していました。対応履歴をきちんと残すため、記録が終わらないと次の電話を受けられない仕組みなのだそうです。
質の高い応対を目指して
特に問い合わせの多い給湯器のリモコンの操作方法については、スタッフが実物を確認しながらお客様にお伝えできるよう、実機を並べた部屋も完備されていました。
取り扱い説明書やマニュアルを読んだだけでは伝えられないような、より具体的なお答えを返せるように、工夫されていることがわかりました。
より質の高い応対を目指すために、コンタクトセンターの閑散期にあたる夏の期間に行われている取り組みが2つあるそうです。
まず一つ目が、スタッフの研修です。
幅広い商品の問い合わせにも答えられるよう、実機研修室が設けてありました。
お風呂、ガスコンロ、レンジフード、給湯器、浴室暖房乾燥機と、ほぼ全ての機器がここに置いてあります。
お客様からの問い合わせは、商品の機能や使い方、施工方法など多岐にわたるため、こうした専門的な知識をつけていくには実機での研修が一番良いとのことでした。
そして二つ目が、業務改善提案のコンテストです。
スタッフがいくつかのグループに分かれ、日々業務を行う中で改善した方が良いと思う点をプレゼンしているそうです。
プレゼン後、各チームを順位付けして、表彰を行っているとのことで、そうした取り組みもスタッフのモチベーション向上につながっているのだと思いました。
また、電話応対コンクールの全国大会にも毎年参加し、スキルアップを目指しているそうです。
カスタマーセンターにかかってくる全ての電話からランダムに取り出した電話応対を評価するという部門で、優秀賞を獲得されたとのことです。
スタッフの方々の日々の努力はもちろん、研修の仕組みや、職場の環境づくりなど、組織全体としての細かな積み重ねと工夫が、こうした結果に結びついているのだと思いました。
貴重なお客様の生の声を、
社内全体で共有する仕組み
ノーリツは、販売会社ではなくメーカーなので、実際に商品を使用されているお客様の生の声を聞くことのできる機会が限られているとのことでした。
そこで、実際にノーリツ製品を利用されているお客様と直接やり取りをしているコンタクトセンターのスタッフが、開発部門にお客様の声をフィードバックする「お客様の声を聴く会」を、定期的に開催しているそうです。
「浴室テレビ用リモコンのボタンが見えにくい」というお客様からの声を受けて、デザインを変更して発売したり、「給湯器のリモコンの文字が見えにくい」というお客様のために、色別にわかりやすいようリモコンに貼るシールを提供したり、よくある質問をまとめた冊子を作ったりと、お客様の声を生かした取り組みをご紹介していただきました。
開発部門だけでなく、あらゆる部門にお客様の声をフィードバックすることで、社内全体の改善を図る「お客様の声検討会」も定期的に開催しているとのことで、コンタクトセンターを通してノーリツグループ全体で、商品やサービスの改善を図られており、「お客様第一」の理念が社内全体でしっかりと共有されているのだと感じました。
おわりに
今回の見学を通して、ノーリツさん・ハーマンさんの、お客様を第一に考える姿勢と、それを実現するための強いこだわりを感じることができました。
また、工場でもカスタマーセンターでも、お客様にもっと満足してもらいたい、良い商品を届けたいとの想いで、社員のみなさまがそれぞれ自発的に改善提案を行っていらっしゃる姿勢が心に強く残りました。
今回の見学にあたり、(株)ノーリツ マーケティング統括部の木村室長、小野リーダー、営業本部の近藤課長、岩崎さん、(株)ハーマン 生産部の方違部長、片山室長、田井室長、梶野室長、商品開発部の中川マネージャー、藤井さんをはじめ、営業・企画・開発部門、各工場、カスタマーセンターなど、本当に多くの方々にご協力いただきました。
こちらからの様々な質問にも丁寧に対応いただき、誠にありがとうございました。
このような貴重な経験を活かし、住宅設備の販売・施工店として、お客様により高品質なサービスをご提供できるよう努力してまいります。何卒よろしくお願いいたします。
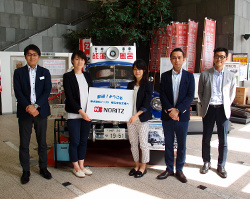